The history of the warehouse is an ancient one – they are said to date back to Egyptian times, when barns to store crops were as much a part of the landscape as pyramids.
English derivation goes back to the 1300s, when the word “warehouse” was first used. For the first mezzanine we need to travel back to the 1570s and haylofts above a stable or cow-shed where hay or fodder could be kept for the animals below.
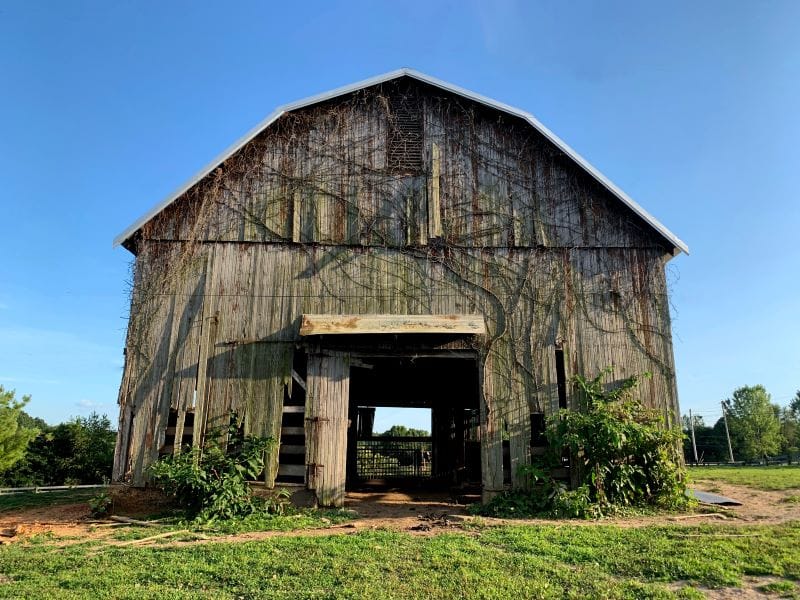
Expanding usable space
Mezzanines and warehouses have gone hand in hand ever since, as people sought to expand their usable space by taking advantage of the height of a building rather than moving into new premises.
Warehouses took a huge leap forward during the Technological Revolution of the 20th century thanks to a boom in scientific discoveries and mass production. The first Automated Storage and Retrieval System was used in a book-club warehouse in Germany and helped streamline the warehousing process with tall vertical storage aisles that allowed faster access to inventory and maximised storage space.
By the 1970s, the invention of mainframe computers led to the first generation of Warehouse Management Systems (WMS) with barcodes to make inventory easier to identify and track. Walmart’s first distribution centre opened in 1971.
Meeting new requirements
The 1970s are when mezzanine structures were introduced in industrial warehouses, as the old idea of the hayloft was repurposed to meet new requirements. Indeed, the expertise of the team at Hi-Level Mezzanines dates back to this decade.
By the mid-1990s, Warehouse Control Systems to automate pieces of equipment, conveyors and carousels were in vogue, and mezzanines were becoming increasingly common in industry, retail and hospitality.
The next evolution in warehousing saw the arrival of Warehouse Execution Systems to carry out inventory control, order management, task creation, picking and packing efficiently so as to manage warehouse workloads.
The second generation of WMS ushered in innovations such as cross-docking to shift inventory from the point of reception to shipping, as well as automated assignment of tasks to employees.
Today some 80% of warehouse operations are taken care of by WMS.
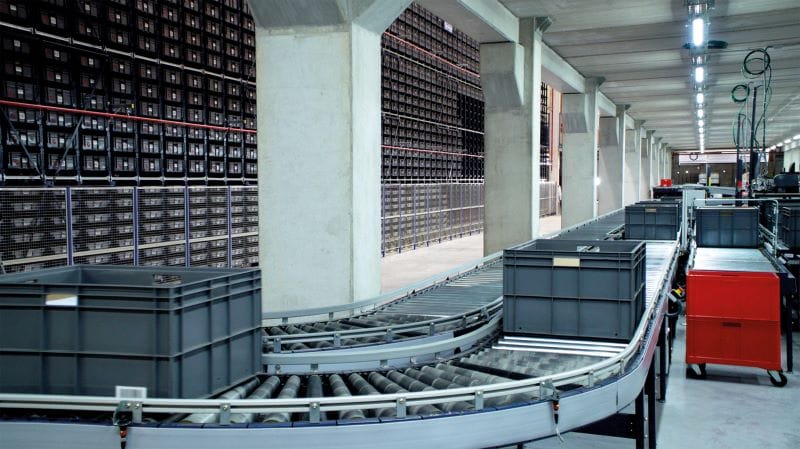
Growth in robotics
Looking ahead, the biggest trend in warehousing is the growth in robotics to serve giant e-commerce organisations.
According to Logistics Manager, automation is essential to fill labour gaps and help the existing workforce, and 88% of European warehouse operatives are expected to have deployed some form of autonomous mobile robots (AMRs) within five years.
AMRs work alongside humans to alleviate some of the pressures of repetitive and demanding physical labour in the warehouse and increasingly we can expect the human workforce to be robotic technicians maintaining the machinery itself. Job satisfaction is likely to rise significantly!
Another advantage of AMRs is that they use sensors to navigate obstacles and people safely, as an alternative to deploying human-operated forklift trucks.
Despite these benefits, “A major hurdle to introducing robotics in warehouses is the installation of dedicated infrastructure,” Ron Farr of Yale told Logistics Manager.
This is where Hi-Level Mezzanines comes in – not just with our 30-year track record in designing and installing mezzanine structures but with our innovative robot-ready flooring system.
Hi-Tile flooring for logistics automation
Our Hi-Tile flooring was created to meet the demands of the booming global logistics automation sector and was launched at IWLEX on 23 May.
It uses robust interlocking 7mm textured PVC tiles to create the most durable, cost-effective flooring on the market. Electrostatic resistance and anti-slip surface make it the perfect partner to robotics solutions. It is already in use by Geek Plus Robotics and with Locus’s Directed Picking technology.
Launch of Hi-Tile comes at just the right time. The global logistics automation market was valued at £30.16 billion and is expected to reach over £93.11 billion by 2027, according to UK Manufacturing, which credits the demand for industrial robots as driving much of that growth.
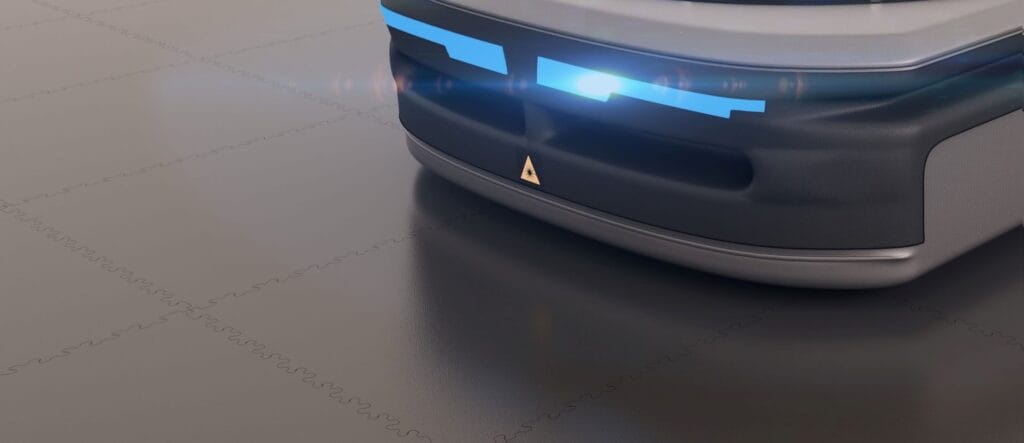
Rise of the super-warehouse
Automation is the key to the rise of Britain’s new breed of super-warehouses, built to service our accelerating online economy.
As The Observer has reported, Dirft – the Daventry International Rail Freight Terminal – near Rugby and Magna Park in Milton Keynes are “town-sized agglomerations, containing thousands of workers, made up of very big sheds.”
Hi-Level Mezzanines has installed mezzanines in such warehouses and distribution centres across the UK, working at a scale that would have been unimaginable when we were founded in 1991.
Our clients feature among the world’s Top 20 biggest warehouses, including Amazon, ASOS, Ikea, M&S and Tesco.
Always ahead of the game
With mezzanines they are making the very best use of their existing space, doubling, tripling or quadrupling their capacity.
And they are confident they can service customer demand into the future without the crippling expense and disruption of moving to new premises.
We have come a long way since Ancient Egypt or the hayloft, and at Hi-Level Mezzanines we are firmly focused on warehouse evolutions to come – always ahead of the game to serve our clients.
If you’re looking to take your business to new heights, get in touch at [email protected] or call 01730 237 190.