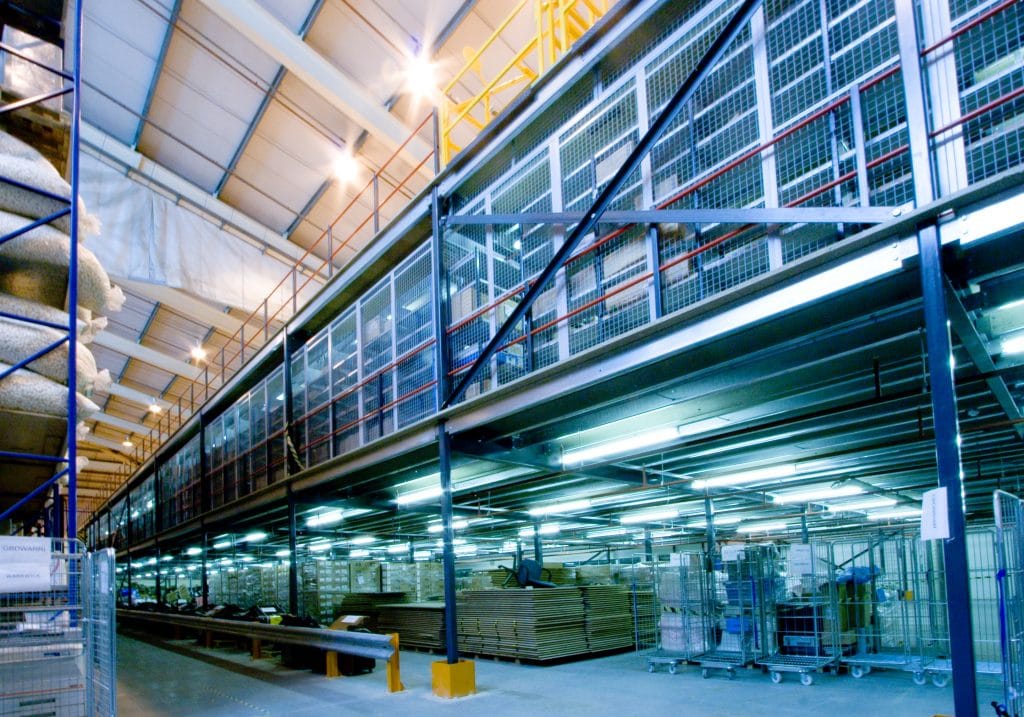
The Challenge
The Technology Division of a major logistics company based in Milton Keynes took the decision to close a 200,000 ft² warehouse facility, from which it had been running an important software supplier contract.
It needed to relocate this part of the business to another existing technology distribution facility in the same town. In order to accommodate the increased business, this facility needed to increase its capacity substantially.
When the logistics company weighed up the options, it became clear that a mezzanine floor within the existing facility would: provide the capacity required, would be cost-effective to install, would improve the productivity of the site and, importantly, the upgraded facilities could be brought on-stream very quickly.
The real challenge however, was to accomplish both the installation of the new mezzanine and the relocation of the warehouse stock to the new facility without disrupting either the existing warehouse operation or the service levels agreed under the software company’s contract.
The Requirement
It was decided to install a two-tier mezzanine to allow for further expansion in the future. This would provide an additional 37,000 ft² of floor area with a loading rating of 5.0kN/m² allowing for storage and light industrial use.
The floors had to incorporate seven staircases and six pallet gates together with full safety protection systems. Before the final specification could be agreed the concrete floor needed to be tested for strength and suitability and then detailed plans would be needed for Building Regulations approval.
In addition to the mezzanine, the main contractor was to be responsible for the efficient installation of all other services including ducting, fresh air, all electrics, fabrication of offices and a board room, 560 bays of shelving and fire protection including a sprinkler system.
The timescale was very tight for a project of this complexity but it was driven by the need to close the existing warehouse facility.
The Solution
The logistics company invited three businesses to tender for the project. Given the complexity of the project and the very tight deadline, the customer needed to partner with a mezzanine manufacturing company that was technically competent, reliable and able to react very quickly.
A Senior Account Manager at Hi-Level’s Distributor said, “In the end it wasn’t a difficult decision to go with Hi-Level. We’ve worked successfully with them in the past so we knew we could rely on them to provide the design and technical support we needed. And, as a leading manufacturer, we also knew that they could handle a project of this scale.”
Hi-Level and their Distributor were ultimately successful in the selection process due to their proactive approach, innovative thinking and flexibility. “It was their willingness to engage with us to identify the project requirements and to make positive suggestions which finally convinced us that they were the right partner for this critical project,” comments the logistics company’s Project Manager.
By the time the selection process had been completed and the necessary guarantees and warranties put in place for the landlord, the maximum site time available before the immovable deadline was just 16 weeks.
In addition to the original project requirements, tests on the concrete floor revealed the need to strengthen it considerably to take the weight of the double floor mezzanine concentrated on columns spaced at 6m intervals.
This meant that 16m piles beneath each column were needed to take the weight of the mezzanine and all this additional work had to be completed within the 16 week period.
Using its unique QD3 Pro mezzanine design management system, Hi-Level developed a programme of work that detailed precisely which elements of the build would be completed by when, and co-ordinated this plan to ensure that the work could be done without undue disruption to the warehouse, which needed to continue normal operations during the construction of the new mezzanine.
The Implementation
Due to the very tight deadlines, channels of communication were kept short with senior level, decision-maker contacts established to ensure that complex issues were identified and dealt with without delay.
Hi-Level took responsibility for producing detailed plans for the mezzanine and then handled all Building Regulations applications and approvals while their customer coordinated all associated services.
In order to comply with strict Health & Safety requirements at the warehouse and out of consideration for neighbouring businesses, the whole work area was protected with barriers, and sheeting was erected to limit the spread of dust from the site works.
All drilling of the concrete slab and piling work was completed by specialist contractors working overnight to limit the impact of noise, vibration and dust and Hi-Level’s installation teams worked in shifts around the clock to ensure that the project progressed according to the schedule.
As soon as the piling was completed at one end of the site, Hi-Level’s mezzanine floor installation teams started the build process working with teams of specialists installing all the other services.
Regular site meetings with all key personnel ensured that as issues were identified they were quickly resolved and, throughout the whole build process, delays were kept to an absolute minimum.
The logistics company Project Manager was delighted with the way the project progressed, “Without the direct lines of communication at all levels from the top down and the willingness to find solutions as issues arose or changes to specifications were needed, this project simply couldn’t have been delivered on time. The flexibility and excellent understanding built up between our teams ensured that the project was delivered on budget and ahead of schedule”.
The Results
The whole project from initial order to completion was delivered in just under 16 weeks. The logistics company has been able to relocate its software contract business in its entirety without any negative impact on service levels for this or any of its other technology contracts.
The consolidation of its technology distribution facilities has produced very significant operational and financial benefits. The relatively low cost of the installation combined with the efficiency gains from greatly increasing the usable space within an existing facility mean that the pay-back period on the investment will be extremely short.
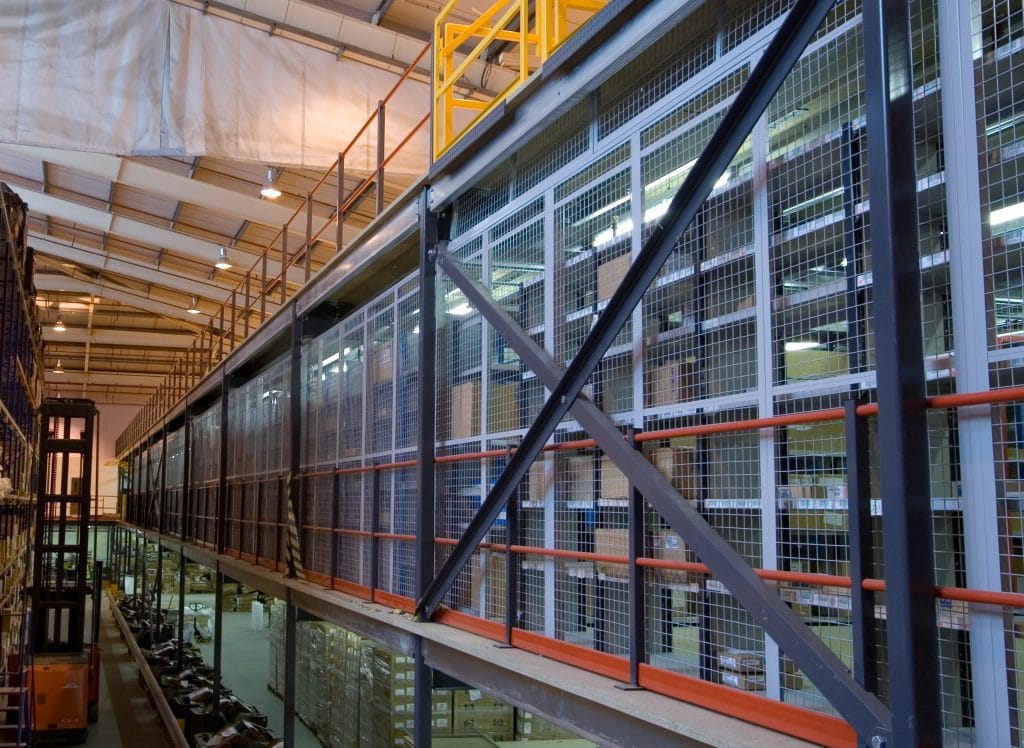
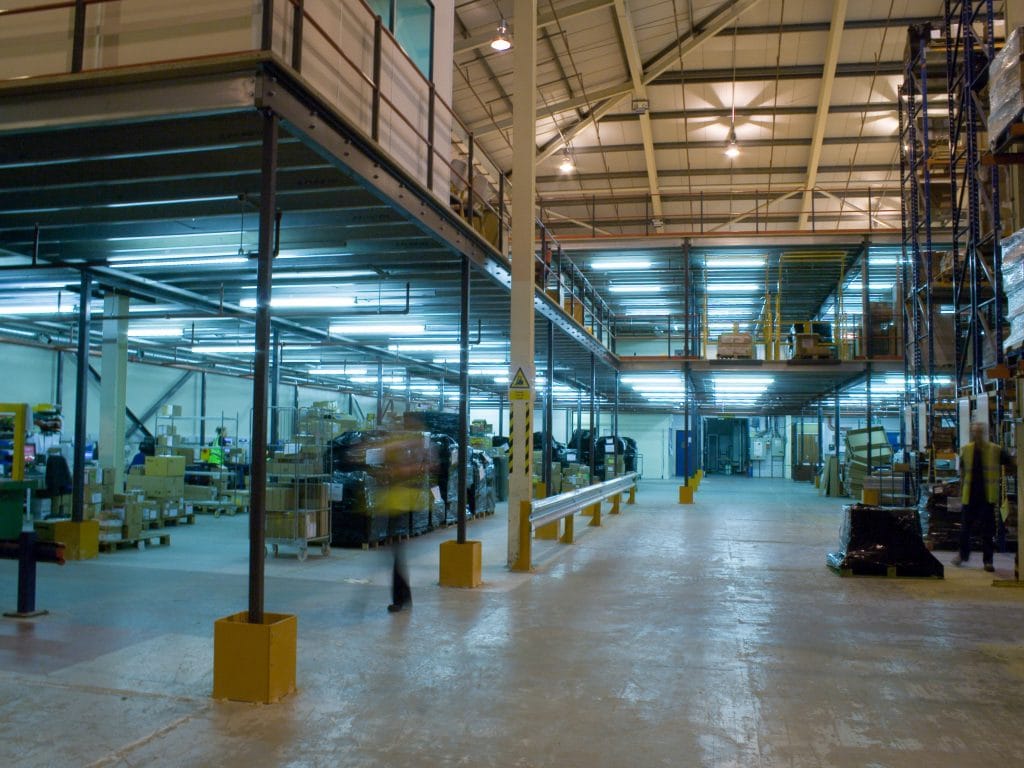
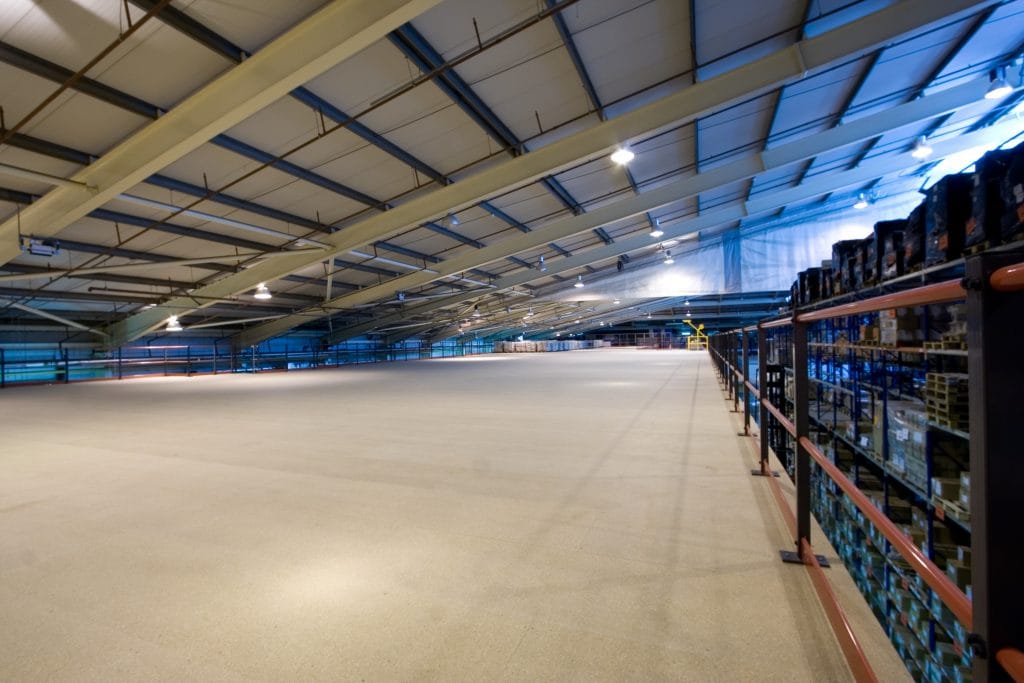
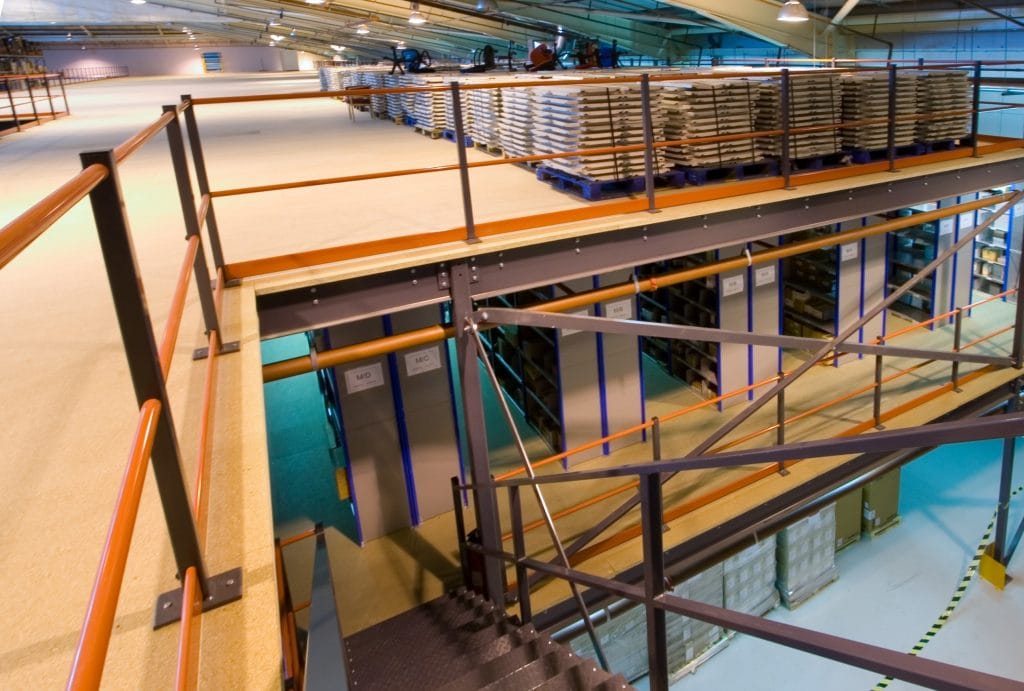
Please get in touch with our sales team if you have any questions regarding previous projects.