Does life have to stop when you install a mezzanine? Clients often have concerns about how they will keep going with their daily business while we are at work putting up their new mezzanine.
Mezzanines are lightweight structures, speedy to install and the best solution to create space in a congested area. It’s natural to want to avoid as much upheaval as possible, however.
And while there will always be some disruption, our 30+ years of expertise at Hi-Level Mezzanines means we can minimise it to make installation as seamless as possible.
Here are seven ways we do it:
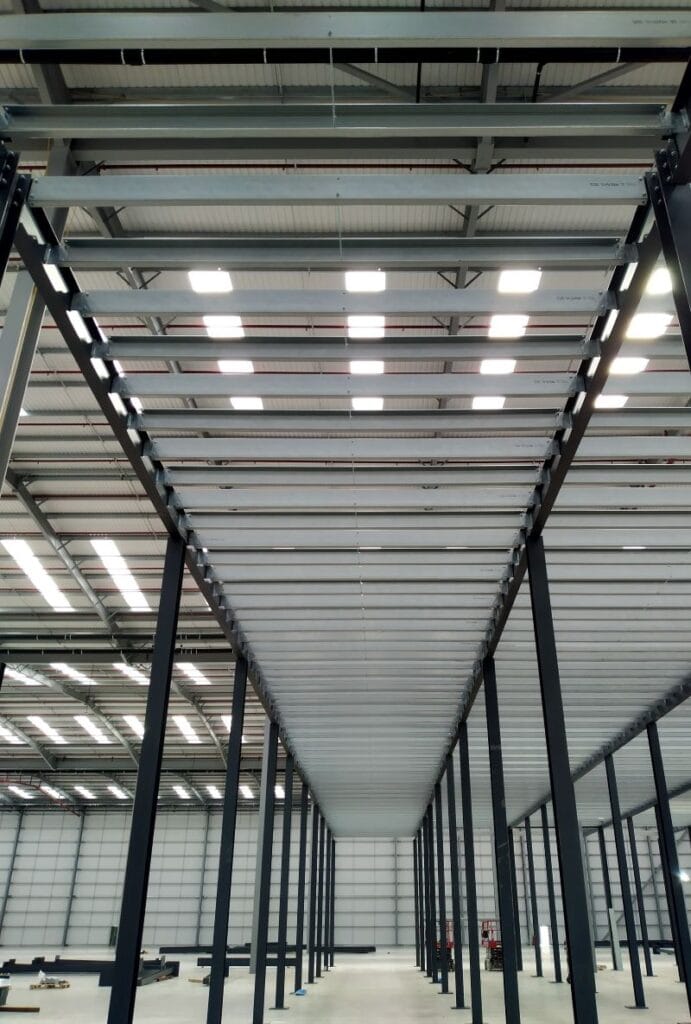
- It is important to understand our customers’ operations and workflow and what they are trying to achieve by putting a mezzanine in. We work as hard to understand the way they use the ground floor as well as their plans for the mezzanine itself.
- As we cannot have clients’ staff in the construction area for health and safety reasons, we have to close it off to them. Clients may move into a temporary space, set up a marquee or shift operations to one end of the building.
- Planning for the installation is crucial. Mezzanines are built in sections and installed bay by bay in a methodical process. We do not need to take over the whole space in one go so our clients can phase operations as construction progresses.
- We encourage future proofing wherever possible. If a client is considering installing more tiers in the future, we advise that we put the skeleton steel structure for the second tier in place at the same time as the first so they only need to add the extra decking when they are ready. We are currently taking this approach with a four-tier mezzanine for a 3PL client in the Golden Triangle to minimise future disruption.
- We work to schedule and are on site when we say we will be. Pinpoint project management is key and we work to clear, concise operations and a planned methodology drawn up in consultation with each client. When we worked on a project with recent project the site was already operational on the ground floor, servicing customers with one-hour deliveries in the first of four such locations around London. We couldn’t be in the way so our accurate timelines were critical!
- We work weekends and out of hours, and programming is vital so that we can be clear about what we can achieve in a ten or 12-hour shift overnight then complete it by the morning. We use different construction approaches to make this possible, for example pinning down columns before the decking is installed to leave a temporary construction that is safe during the client’s working hours.
- We carefully choose the best season to install each client’s mezzanine – avoiding the Q4 run-up to Christmas for hyper-busy retailers, for example. We will instead advise a non-peak time when the client is holding less inventory and fewer goods are going out of the door. It makes the whole installation process simpler for everyone.
Hi-Level Mezzanines
For more than 30 years Hi-Level Mezzanines has been creating space for amazing things to happen.
The company is an independent supplier of mezzanine flooring solutions with a value-engineered design model that optimises steel utilisation and drives costs down.
It provides mezzanine floors of the highest quality in the industry, thanks to the expertise of a team of qualified structural engineers, an innovative digital design process, an established and trusted supply chain, and advanced solutions.
If you’re looking to take your business to new heights, get in touch at [email protected] or call 01730 237 190.