While supply chains have taken a battering over the past three years – with the war in Ukraine piling on the misery after the pandemic, following the turbulence of Brexit – there could be an answer for your business.
It is true that movement of goods is at the mercy not just of global disruption, but also strikes at home and laudable efforts to reduce environmental impact.
Which is why the “Just in Case” model of mitigating supply chain crises is now firmly replacing the “Just in Time” model favoured before Covid.
The answer to these challenges comes from the part that mezzanines can play in making businesses more resilient.
Installing mezzanines allows a company to double, triple or even quadruple its usable space, permitting more stock to be held on site so it can better withstand supply chain fluctuations.
That means the reassurance of being able to keep serving customers and minimising the dangers of unexpected shortages, missing supply deliveries, last-minute substitutes and quality failures.
At Hi-Level Mezzanines we have the robust processes in place to ensure that we provide our clients with an unrivalled service.
In the words of our client Beryl, the nationwide bike- and scooter-sharing scheme: “The whole process from quotation to installation was handled smoothly in a turbulent market.”
This capacity is even more valuable in the face of 3 supply-chain trends:
- Global instability
As John Manners-Bell, CEO of Transport Intelligence Insight told Logistics Manager magazine: “From operational risks such as border delays, to traffic congestion, industrial action, cybercrime and the rising cost of oil, supply chain managers must be prepared for daily disruption.” Add Ukraine to that list and it is no surprise that 85% of UK companies are planning to move from “Just in Time” to “Just in Case”, according to enterprise software company SAP.
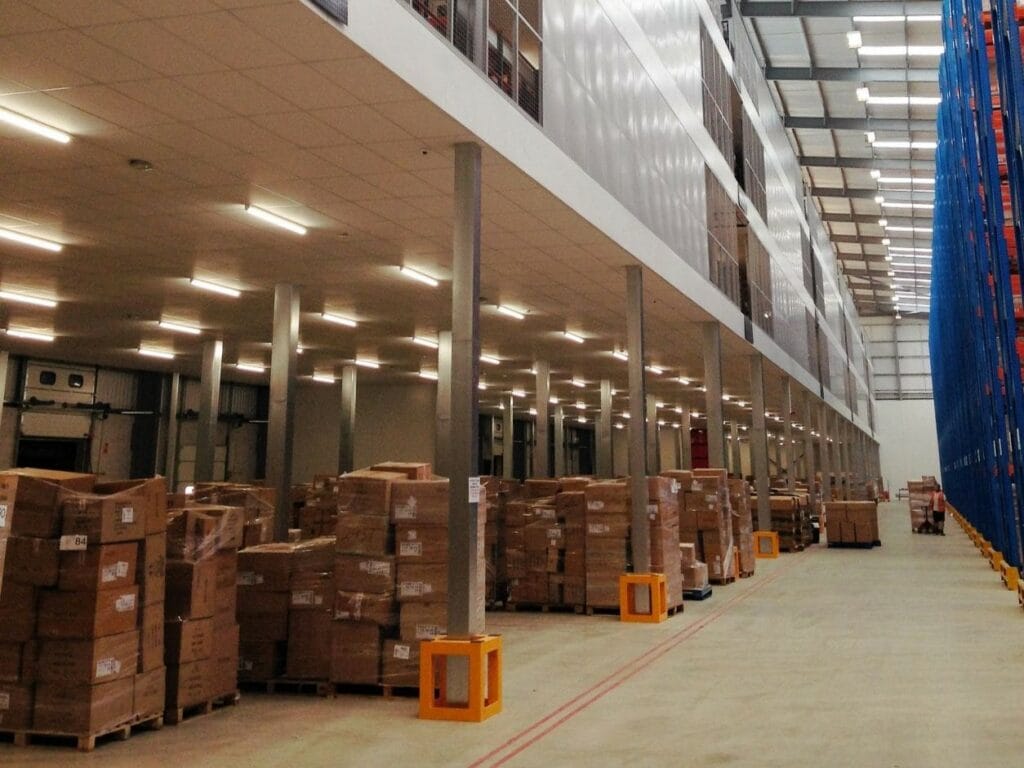
- Strikes
At the port of Liverpool 600 workers have carried out four weeks of strikes over pay and job insecurity since September, while days of action by 1,900 workers at the port of Felixstowe, the UK’s largest container gateway, have been held since August. This has led to vessel diversions, delays and cancellations to cargo. Even Waitrose has been suffering from empty shelves.
With Southampton and London Gateway ports working at capacity, container shipping lines have been offloading UK-bound cargo at hubs such as Antwerp and Rotterdam (with knock-on additional costs for fuel and driver hours.) Strikes and threats of walk-outs are ongoing at German ports.
“Even minor interruptions to port operations can have a major impact on container line network efficiency and cause a domino effect up and down supply chains. Strikes at European ports this year have already been highly damaging to logistics operations, manufacturers and industry at large. We expect further industrial action to be just as harmful,” Christian Roeloffs, CEO of Container xChange, told Freight Forwarder magazine.
- Environment
Some companies are holding onto stock longer so they can be more efficient in their delivery schedule, saving CO2 impact by re-organising routes and delivering less frequently. Rather than ordering a small truck of goods to arrive once a week, their customers are placing a bigger order once a month and likewise storing extra stock. It makes sense both for carbon footprint and reducing costs. Another consumer trend is how Amazon customers, for example, are opting for sustainable – i.e. fewer – deliveries. Installing a mezzanine to hold additional goods makes all this possible.
How Hi-Level is taking the lead
At Hi-Level our robust processes and planning mean we have been able to stave off supply chain woes and improve our service to our clients.
Whereas during the pandemic our lead times were 12 weeks from signing off drawings to starting work on site, these are now down to an impressive 3 ½ weeks.
With the challenges the industry has faced in the past few years we are particularly proud of testimonials such as this, from the Project Manager at GB Racing: “Impressed with Hi-Level’s technical assistance and guidance throughout the project. Even delays due to steel shortages caused by the Covid-19 pandemic were managed as well as possibly could be”.
Contact us today for more information at [email protected] or call 01730 237 190.