Hi-Tile Flooring Enhances Robotics Efficiency in E-Fulfilment Centre
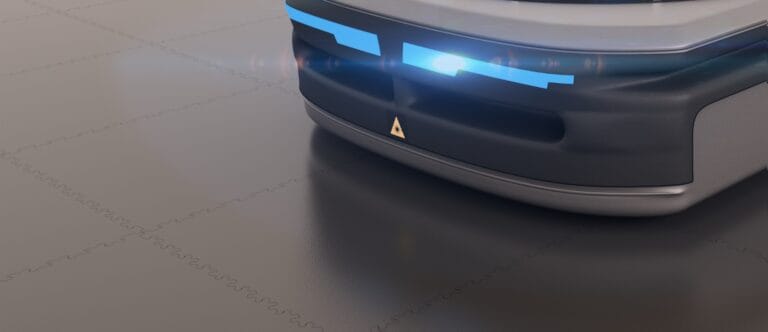
Hi-Level’s Hi-Tile flooring helped a global health & beauty retailer enhance their e-fulfilment centre with robotics. Durable, quick to install, and easy to maintain, the solution supported high-volume operations with zero tile replacements to date.