Why smart-thinking firms are installing mezzanines in Yorkshire and the North East
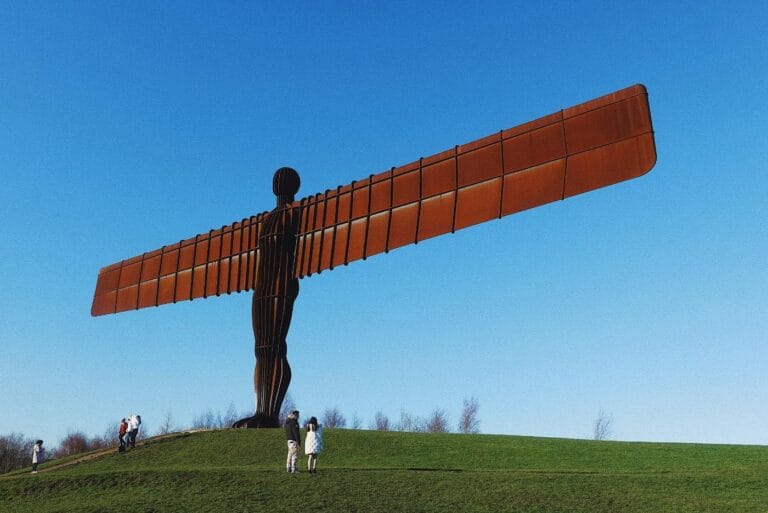
Superb transport links along with a skilled and diverse workforce make Yorkshire and the North East an attractive location for logistics and manufacturing businesses – and mezzanines are helping them overcome a low warehouse vacancy rate. Two of the UK’s…